Micromanipulators for patch clamp, Neuropixel recordings and more
Our uMp micromanipulators are designed with demanding applications in mind. From patch clamp to in vivo recordings with silicon probes. Wherever smooth motion is key.
Built on cutting edge technologies, uMp micromanipulators afford significant stability and accuracy, outperforming traditional stepper motor alternatives on all performance characteristics. In addition, the integrated technology enables automated microelectrode- and pipette techniques. Taken together, this means that uMp micromanipulators make electrophysiological recordings more reliable and reproducible, removing unnecessary headaches from challenging experiments. No matter if you are looking for a manipulator for patching, Neuropixels or other neuronal probe.
Why use Sensapex micromanipulators?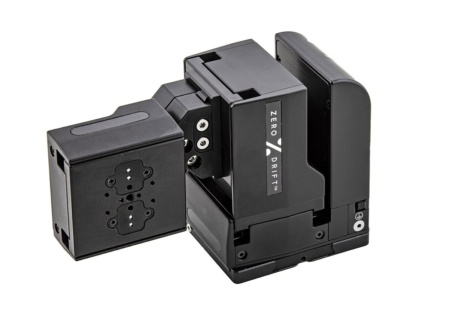
- Integrating our patent protected ZERO DRIFT™ technology, the uMp is the most stable electrophysiology micromanipulator on the market – making pipette drift a thing of the past.
- Closed-loop piezo motion on all axis makes the uMp the most accurate electrophysiology manipulator on the market – ensuring electrodes end up exactly where they need to be. Every time. No matter if controlled by hand or automated.
- Ultra compact – the small size makes the uMp an perfect fit for efficient use of space. Which means that more manipulators can be positioned around the sample.
- With plug & play installation and an intuitive touch-screen interface, uMp micromanipulators are easy to use. Less distractions and time lost on configuration leaves more time and attention for experiments.
- The manipulators can be run completely from battery, minimizing electrical interference – for the lowest possible noise recordings.
How do our manipulators achieve this performance?
All of uMp micromanipulators are based on our unique and patented ZERO DRIFT piezo-technology. Here, a piezo motor moves an axis to the required position. Once this is reached, the motor is powered off and the position is maintained by a strong friction force, which clamps the axis. As a result, the linear position stays exactly the same with zero drift during static external loading conditions and constant temperature.
Each axis has an integrated linear position sensor with 5 nm resolution. With this sensor, the position of each axis is continuously measured in real time. This allows users to confirm that the manipulator is indeed not drifting. More importantly, during axis movement the sensor provides feedback on the current position of the axis, ensuring that the movement stops exactly when the desired position is reached. This closed feedback loop is what enables the uMp manipulators to achieve their industry-leading repeatability and accuracy.
All of this motion control is integrated within the micromanipulator itself. This means that each has a microprocessor and memory and is running a real-time operating system. This allows a single touch screen and multiwheel unit to control a nearly unlimited number of manipulators (actually 65,536).
Overview of our micromanipulator products
- The uMp-TSC2 touch screen unit provides an intuitive and stand-alone user interface that is used together with uMp-RW3/4 wheel controllers. In addition to basic operation with manipulator selection and speed setting, many unique features are offered like customizable wheel-to-axis and movement direction definitions, absolute vs. relative coordinate views, 1-click re-configurable memory positions, virtual axis use and automated pipette cleaning for immediate re-use. All functions and configuration options for the full device range is provided by this small unit – no additional PC is required for setup and use.
- Each uMp-TSC2 connects to a uMp-HUB, Each uMp-HUB can connect four uMp micromanipulators. The standard HUB includes a Li-ion battery to power the connected manipulators, whereas the HUB lite does not include a battery. There is no practical limit on how many uMp-HUBs and uMp micromanipulators can be connected to one system, providing unlimited scalability. For PC control only applications, the HUB can be connected to a PC directly, without the need for a TSC2.
- uMp micromanipulators are available as three axis uMp-3 version that has 4th virtual axis and as uMp-4 version with four physical axes. uMp-3 is commonly used for in vitro work, whereas uMp-4 is often selected for in vivo experiments, where steep approach angles are required, making the 4th physical axis necessary.
- Further standard accessories include manipulator bases with convenient mechanisms to aid pipette exchange, as well as versatile selection of adapters for attaching amplified head-stages and rod like items. In particular, we have full selection of Neuropixel probe holders available at our webstore (including the new 2.0 versions).
We facilitate new discoveries
Sensapex has had the privilege to provide products to more than 1000 labs worldwide. We are regularly surprised and impressed by the clever way in which our manipulators are used for experiments. Often in ways that we never imagined. Our ever-growing list of References showcases some of the amazing work being done with our instruments.
Configuration examples
Classic single micromanipulator system for patch-clamp
-
- uMp-TSC2 touch screen controller
- uMp-HUB lite
- uMp-RW3 rotary wheel unit
- uMp-3 micromanipulator
- uMp-DVT headstage adapter
- uM-GND-1 grounding cables
Get a quote
Single micromanipulator system for in vivo electrophysiology and/or optogenetics
-
- uMp-TSC2 touch screen controller
- uMp-HUB (or HUB lite)
- uMp-RW4 rotary wheel unit
- uMp-4 micromanipulator
- uMp-RHL rod-holder adapter
- uM-GND-1 grounding cables
Get a quote
Dual micromanipulator system for patch-clamp
-
- uMp-TSC2 touch screen controller
- uMp-HUB (or HUB lite)
- uMp-RW3 rotary wheel unit
- uMp-3 micromanipulators, 2 pc
- uMp-DVT headstage adapters, 2 pc
- uMp-ROT rotation stand modules, 2 pc
- uM-GND-1 grounding cables, 2 sets
Get a quote
Sensapex products are proprietary and patented (US 9,138,892, US 9,662,783, EP 2 776 215, US 10,427,292; EP 09851052.2, EP15906190.2, US 15/765,608, EP: 15906189.4). Automated patch clamp (US 9,498,293 and US 9,668,804) and pipette cleaning (US 15/232,770 and EP 16836035.2) products are manufactured under licenses from GTRC and MIT, U.S.A.
uMp-TSC2 Touch Screen Controller
Connectors for micromanipulators | 4, via HUB unit |
Batteries | None, but optional in HUB unit |
AC power supply | 90-264 V, 50-60 Hz |
Dimensions | 127 x 126 x 99 mm |
Get a quote
uMp-HUB and HUB-Lite
Connectors for micromanipulators | 4 pc |
Batteries (not included in Lite variant) | Li-ion (rechargeable), up to 1 week usage time |
AC Charger | 90-264 V, 50-60 Hz |
Dimensions | 95x95x52 mm |
Get a quote
uMp-RW3 Rotary Wheel Remote Interface
Connection to uMp-TSC touch screen controller | USB-cable, included |
Dimensions | 169 x 168 x 54 mm |
Get a quote
uMp-RW4 Rotary Wheel Remote Interface
Connection to uMp-TSC touch screen controller | USB-cable, included |
Dimensions | 169 x 168 x 54 mm |
Get a quote
uMp-3 Triple axis micromanipulator
Positioning range | 20 x 20 x 20 mm3 (XYZ) |
Resolution / repeatibility: | 5 nm / 100 nm |
Max. speed | 5 mm/s |
Load | 0–150 g |
True approach angle | 0–45 degrees |
4th axis: | virtual |
Table mounting: | Bolt |
Electrode exchange**: | Side rotate | flip + slide |
Dimensions: | 128 x 49 x 77 mm |
Get a quote
uMp-4 Four axis micromanipulator
Positioning range | 20 x 20 x 20 x 20 mm3 (XYZD) |
Resolution / repeatibility: | 5 nm / 100 nm |
Max. speed | 5 mm/s |
Load | 0–150 g |
True approach angle | 0– 90 degrees |
4th axis: | Physical |
Table mounting: | Bolt |
Electrode exchange**: | Side rotate | flip + slide |
Dimensions: | 136 x 49 x 104 mm |